What is
Material Jetting?
What is
Material Jetting?
A comprehensive guide to Material Jetting
Material Jetting (MJ) speeds up the testing and go-to-market phase. It is used by a multitude of industries such as automakers, design firms, art studios or medical organisations to create reliable prototypes with a high level of accuracy. The process creates 3D prints with multiple material parts, colours and a smooth surface finish.
Material Jetting can be divided into several techniques, of which the most important ones are NanoParticle Jetting (NPJ) and Drop-On Demand (DOD). This article offers all relevant information on the Material Jetting process, materials used, advantages, drawbacks and how it can enhance the production processes of your organisation.
What is Material Jetting?
Material Jetting belongs to the 7 types of Additive Manufacturing (AM) technologies along with Vat photopolymerization, Binder jetting, and others.
In the material jetting process, droplets are jetted onto the build platform of the 3D printer and cured by ultraviolet light or heat. It is often compared to the 2D ink jetting process, as the material droplets are selectively deposited to create three-dimensional objects layer by layer.
The material deposition is controlled by X, Y and Z movement. Required support material is often printed simultaneously and built from a dissolvable material. After printing, the material can be easily removed during post-processing without leaving traces.
Material Jetting is used by product manufacturers due to its high accuracy, with a dimensional accuracy of ± 0.1% and a lower limit of ± 0.1 mm to 0.02 m. Typical build sizes include 380 x 250 x 200 mm and can even reach dimensions of 1000 x 800 x 500 mm.
Material Jetting is regarded as one of the fastest as well as one of the most accurate 3D printing technologies. Manufacturers have developed different types of material jetting for different applications. However, even though there are different types and applications, Material Jetting follows a common principle.
Types of Material Jetting (MJ)
Material Jetting is a highly popular process, as it allows to integrate multiple material parts and colours in one single printing. This saves time and creates realistic prototypes. Material Jetting can be done in multiple ways, which are patented by different companies. The choice of the right process type mainly depends on your desired outcome.
Material jetting can be used for a combination of multiple materials. NanoParticle Jetting (NPJ) is the best option when you need to manufacture multiple small parts at once. Drop-On Demand (DOD) is the preferred choice of the jewelry industry. The following sections explain each type in detail.
The core material jetting technology, or PolyJet, used the very first printer by Object (later Stratasys). Material jetting technology jets ultra-thin layers of liquid photopolymer material onto the build tray, which can be compared to traditional inkjet printing. Each layer is immediately cured by UV light, so that the following layers can be built upon. Support materials can be used for complex geometries and are easily removed afterwards, either by hand or by water jetting. Material jetting parts can be a combination of rigid or flexible, colourful or clear materials, which may even be used for medical purposes. The 3D prints offer final product realism at granular detail.
Drop-On Demand (DOD)
The Drop-On Demand (DOD) process uses a wide range of materials such as wax instead of photopolymers. DOD printers have two print jets for build material as well as dissolvable support material. One big advantage of the system is its ability to print high resolution curves as well as a perfectly flat surface by skimming each completed layer with a fly cutter. This leads to precise and accurate results. The application is used by industries such as jewellery to create high-precision printing and moulds.
NanoParticle Jetting (NPJ)
Nano Particle Jetting (NPJ) is an advanced 3D printing technology that is used to create complex and high-resolution objects by jetting tiny nanoparticles of material onto a build platform. It is a relatively new additive manufacturing technique that offers unique advantages in terms of precision, materials versatility, and resolution.
NPJ can work with a variety of materials, including metals, ceramics, polymers, and composites. Different jetting materials can be mixed together to create customized material properties for specific applications.
What is material jetting and what are its core features?
The main components of printers consist of print heads, UV lights, the build platform as well as material containers. Material Jetting enables companies to create multi-material & full-color printings layer by layer, resulting in realistic prototypes that have very smooth surfaces.
What materials are used with Material Jetting?
Material Jetting uses 3 main material types when it comes to 3D resins: Base resins, composite resins and support material.
Base resins
These resins can be used without any combination and can be separated according to their specific properties. Base resins may include general-purpose, transparent, strong, flexible, biocompatible or castable resins, just to name a few. Each specific property can have its own advantages and disadvantages when it comes to the specific application.
Composite resins
Composite resins can consist of many different base resins, so manufacturers need to have a profound knowledge about all properties when mixing the right ingredients. The choice of mixture also depends on the capabilities of the machine to handle different material containers.
Support material
Support resins are optimized to be easily removed from the print. For this purpose, dissolvable materials are used. Different support materials have different properties when it comes to solubility. Depending on the support material used, it might even be possible to remove it manually and with a water jet.
The advantages and disadvantages of Material Jetting technology
Material Jetting is a popular 3D printing process with a high level of accuracy, which makes it popular for highly realistic prototypes, injection moulds, investment castings and medical devices.
Designers can take advantage of Material Jetting’s multi-material, multi-colour capabilities, while the medical industry is able to produce anatomical models for surgical planning and training.
When it comes to low-volume moulds and patterns for certain industries, Material Jetting can even be a cost-efficient alternative to traditional tooling. However, next to its multiple advantages, Material Jetting does not suit all purposes. The following sections summarize the most important advantages of disadvantages that Material Jetting has to offer.
Advantages of Material Jetting
One of the biggest advantages of Material Jetting is the high level of resolution and accuracy. Each layer can be printed up to 0.013 mm, which leads to a smooth finish and accurate features. Support materials also don't leave marks after removal. The results are realistic objects, intricate shapes as well as sharp edges.
Further, Material Jetting is able to layer many materials and colours, as printers can incorporate multiple nozzles. Depending on the goals, companies can achieve multiple properties such as translucency, opaqueness, rigidity or flexibility of the 3D print. Therefore, companies can create highly realistic prototypes, mould manufacturing, investment castings and even medical devices.
Disadvantages of Material Jetting
Next to its multiple advantages, Material Jetting comes with its own limitations compared to other printing techniques. First of all, the required equipment is expensive and the process to create the raw materials for 3d printing is relatively slow, as the structures are built one droplet at a time. Material Jetting produces relatively weak models, which can become a problem when the functionality of the prototype plays a crucial role.
The support structures offered by Material Jetting are solid, which adds up production costs. Further, limited materials such as wax are relatively fragile and expensive. The number of viscous materials is also limited.
Conclusion
Material Jetting offers highly precise and colorful models, which can speed up time to market and reduce production costs. With its multiple applications and user scenarios, many industries have been profiting from this advanced Additive Manufacturing (AM) technology. If you plan to reduce your tooling costs or need precise-looking prototypes, Material Jetting process might be the right approach.
FAQ
Q1: What is Material Jetting and its significance in various industries?
A1: Material Jetting (MJ) is an Additive Manufacturing (AM) technology used across industries such as automotive, design, art, and healthcare. It accelerates the testing and production phases by creating accurate prototypes with multiple material parts, colors, and smooth surface finishes.
Q2: How does Material Jetting work and what are its key features?
A2: Material Jetting operates by jetting droplets onto a build platform, subsequently cured by UV light or heat, resembling the process of inkjet printing but in three dimensions. Its key components include print heads, UV lights, the build platform, and material containers, enabling the creation of multi-material, full-color prints layer by layer, resulting in realistic prototypes with exceptionally smooth surfaces.
Q3: Which materials are utilized in Material Jetting?
A3: Material Jetting uses three main types of 3D resins: Base resins (e.g., transparent, strong, flexible), Composite resins (mixes of base resins), and Support materials (easily removable materials like dissolvables). These materials enable diverse properties in the printed objects, depending on specific application requirements.
Your personal contact
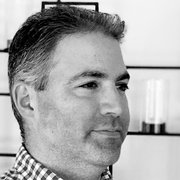
Christopher Cocklan
3D Printing Business Development Manager EnergyCuring
RAHN USA Corp.