3D Printed
Surgical Instruments
3D Printed
Surgical Instruments
3D Printed Surgical Instruments and 3D Printed Medical Tools: A Comprehensive Overview
3D printed surgical instruments and 3D printed medical tools are transforming healthcare by offering highly customised, patient-specific solutions. Even better: These innovations enable greater precision in surgeries, improve outcomes, and reduce the time and cost associated with traditional manufacturing.
This article takes an in-depth look at how additive manufacturing (AM) is shaping the medical landscape.
Types of 3D Printed Surgical Instruments
Additive manufacturing (AM) has been revolutionising the medical landscape for years, from 3D printing in dentistry to 3D printing in healthcare, as it offers more flexibility, speed, and customization compared to traditional manufacturing methods.
Most common 3D printed surgical instruments and 3D printed medical tools include:
- Scalpels: Precision 3D printing enables sharp, disposable blades designed for specific procedures, reducing infection risks.
- Forceps: Printed with intricate, customizable grips, these tools offer enhanced control and can be tailored for tasks like tissue handling.
- Clamps: Used to control blood flow, 3D-printed clamps are lightweight and can be adapted in size or shape to accommodate different anatomical needs.
- Retractors: These instruments keep surgical areas open. 3D printing allows for bespoke designs that minimise tissue damage and improved access.
Benefits of 3D Printed Surgical Instruments
3D printed surgical instruments offer several key benefits that are transforming healthcare, including custom designs, faster production at a lower cost, enhanced surgical outcomes as well as an overall improved patient care.
Customization and Personalization of Instruments
3D printed medical tools can be designed to fit the exact anatomical requirements of individual patients, which enables surgeons to perform with greater accuracy and efficiency.
As a result, these instruments reduce the risk of complications by aligning perfectly with the specific anatomical needs of each patient, which reduces tissue trauma and leads to faster recovery times as well as less postoperative discomfort.
Rapid Prototyping
Rapid prototyping allows designers and engineers to quickly transform digital concepts into physical models for rapid testing, evaluation, and refinement of ideas. This process dramatically shortens development times while reducing costs associated with traditional prototyping.
As adjustments can be made in real-time, designers can refine products based on immediate feedback and create a more efficient workflow, which ultimately reduces time to market.
Cost-Effectiveness and Accessibility
By reducing the need for traditional moulds and tooling, 3D printing significantly lowers production costs, especially for small-batch and custom items. This makes it possible to create affordable, personalised solutions that were previously too costly.
3D printers can operate in various environments, which makes them accessible even in remote or resource-limited areas, such as field hospitals or rural clinics. With the ability to produce items on-demand, 3D printing minimises waste, optimises resources and makes advanced tools more available to a broader population.
Enhanced Surgical Outcomes and Patient Care
With custom-designed 3D printed surgical instruments, surgeons can plan and perform procedures with greater precision, tailored to each patient’s unique anatomy. This precision reduces the likelihood of complications, minimises tissue damage, and shortens recovery times.
3D printed medical tools can be personalised for better fit and function. By enabling more accurate and efficient surgeries, 3D printing technology supports better patient outcomes and enhances the overall standard of care.
Challenges and Future Directions
Besides its prospects, additive manufacturing for 3D printed surgical instruments still faces various challenges when it comes to the material choice and fulfilment of regulatory standards.
Medical tools must be durable enough to handle repeated use without compromising performance, while also being biocompatible to prevent adverse reactions in patients. Sterilisation adds another layer of complexity, as materials need to withstand high temperatures, chemical exposure, and radiation without degrading.
RAHN: Your Reliable Partner for 3D-Printed Surgical Instruments and 3D-Printed Medical Tools
Creating 3D printed surgical instruments requires specialised materials to meet medical standards. As your reliable supply partner of raw materials for 3D printed medical tools, RAHN has the knowledge and expertise to make your product a success.
Contact us and we will be glad to assist you.
Your personal contact
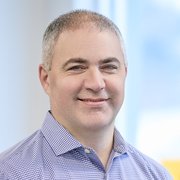
Christopher Cocklan
3D Printing Business Development Manager EnergyCuring
RAHN USA Corp.