3D Printing
on Solid-State Battery Development
3D Printing
on Solid-State Battery Development
The Impact of 3D Printing on Solid-State Battery Development
Stereolithography (SLA) has become a common way to produce parts of solid-state batteries. The versatile usage of photopolymers allows manufacturers to streamline production while saving costs and increasing quality. This technology, which has revolutionized industries like 3D printing in healthcare, is now paving the way for innovative advancements in battery development.
The following sections provide you with a bird’s eye view of 3D printed batteries, the challenges, advantages and common production methods.
What are solid-state batteries?
Solid-state batteries are a type of battery technology that utilises solid electrolytes instead of the liquid or gel-like electrolytes found in traditional lithium-ion batteries. Solid electrolytes, often made of ceramics or polymers, replace the flammable liquid electrolytes and enhance safety by reducing the risk of leakage or combustion.
The anode and cathode in solid-state batteries can also leverage advanced materials like lithium metal or sulphur to improve energy density.
This design allows for higher energy storage capacity compared to conventional batteries. Moreover, solid-state batteries exhibit a wider operating temperature range, making them suitable for various environments.
The advantages of solid-state batteries have spurred interest in numerous applications and industries, including electric vehicles for their enhanced range and faster charging, consumer electronics for longer-lasting devices, and medical devices for their safety and reliability.
The challenges of solid-state battery development
When introducing new technologies and battery production methods, manufacturers face critical challenges, including production costs, optimising the energy and life cycle as well as materials and safety concerns.
Production costs
Developing specialised materials that meet the demanding requirements of solid-state batteries can be costly. Moreover, the equipment needed for precise SLA printing might require substantial investments, which can initially increase the overall production cost of these batteries until the investment pays off.
Despite the decrease in battery production costs over the years, there is still an opportunity to further reduce the price. These opportunities can be found throughout the entire value chain, for example through process and production improvements as well as an increased performance.
Energy and cycle life
When producing solid-state batteries, energy density and cycle life are crucial factors. The question remains of how to boost power capacity while simultaneously enhancing power storage capabilities. SLA printing can enable the production of intricate designs, potentially allowing for increased energy density by precisely controlling the internal structures of battery components.
However, challenges like material compatibility and structural integrity can impact the cycle life. Ensuring the stability of the printed components over numerous charge-discharge cycles is essential. Optimising SLA printing parameters, selecting suitable materials, and addressing structural durability concerns are key to achieving high energy density while maintaining a prolonged cycle life.
Materials
Materials pose significant challenges in the development of 3D printed batteries. Finding suitable solid electrolytes that offer high conductivity while being chemically stable and mechanically robust is crucial. Many materials that are promising under laboratory conditions might face scalability or cost challenges when produced on a larger scale.
Additionally, identifying compatible electrode materials that work effectively with solid electrolytes, providing high energy density and stable cycling, remains a hurdle. Balancing these material requirements – conductivity, stability, scalability, and cost – is a primary challenge in advancing solid-state battery technology.
Safety
Solid-state batteries are subject to stringent safety standards to ensure their reliable and secure operation. These safety standards include thermal stability, electrical safety, mechanical durability as well as chemical compatibility.
Meeting these safety standards is crucial for the adoption of 3D printed batteries across industries like automotive, electronics, and energy storage. Adhering to these regulations ensures that solid-state batteries offer a safe and dependable energy storage solution.
Creating solid-state batteries using SLA
Creating solid-state batteries using SLA Battery manufacturers make use of Stereolithography (SLA) and photopolymers to streamline the production processes of particular battery parts. These parts include complex housing structures, internal architectures, as well as custom electrode designs.
Complex housing structures
SLA enables the creation of complex housing structures with exceptional intricacy and accuracy. Its ability to fabricate custom designs and precise geometries allows for internal layouts, optimising the arrangement of components within the battery. This intricate housing design has the potential to enhance the functional efficiency and performance of 3D printed batteries. The precision offered by SLA printing contributes to accommodating specific design requirements for improved functionality and performance.
Internal architectures
SLA is able to craft internal architectures within battery cells, refining pathways for the movement of ions. Its precision allows for the creation of custom-designed structures, which optimise the routes for ion transfer within the battery. These internal designs enhance the efficiency and facilitate faster and more controlled transmission between electrodes. The capability to print intricate internal structures plays a pivotal role in maximising the performance and efficiency of solid-state batteries, as it promotes a better energy transfer.
Custom electrode designs
SLA can generate moulds, prototypes, or models for electrolytes, anodes, or cathodes within solid-state batteries. These precise replicas allow for detailed testing and optimization before the actual component production with alternative manufacturing methods. By leveraging SLA's accuracy in producing detailed designs, engineers can refine and fine-tune custom electrode structures, ensuring optimal performance and functionality. This approach enables thorough experimentation and validation of electrode designs before scaling up production.
Other printing methods used for creating 3D printed batteries
Apart from Stereolithography (SLA), there are various printing methods for 3D printed batteries. These technologies use different processing techniques and require different raw materials for 3D printing.
Selective Laser Sintering (SLS) uses a laser to fuse powdered materials to produce battery components. SLS for 3D printing batteries involves using powdered materials, typically metal powders or specialised polymers, to create battery components such as electrodes, casings, or structural elements.
Direct Ink Writing (DIW) can precisely extrude inks or pastes, allowing the deposition of intricate and customised patterns layer by layer to form electrode structures, electrolytes, or other battery elements.
Electron Beam Melting (EBM) and Laser Powder Bed Fusion (LPBF) utilise metal powder fusion via directed energy beams, which is suitable for producing metal-based battery components.
Conclusion: 3D printing has the potential to innovate solid-state battery development
3D printing holds immense potential in revolutionising the development of solid-state batteries. Its versatility in creating intricate designs, customising internal structures, and producing complex components offers unprecedented opportunities for advancing battery technology.
Together with other printing technologies, SLA advances the ability to iterate quickly through prototyping and create tailored architectures to optimise energy density, cycle life, and safety in solid-state batteries.
As 3D printing solutions and methods continue to evolve, they are poised to drive innovation, accelerating the development of safer, more efficient, and higher-performing solid-state battery solutions for various industries.
Your personal contact
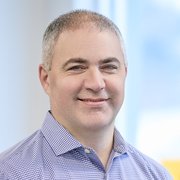
Christopher Cocklan
3D Printing Business Development Manager EnergyCuring
RAHN USA Corp.