Adding Colorants
Into Resin Materials for 3D Printing
Adding Colorants
Into Resin Materials for 3D Printing
Adding Colorants Into Resin Materials for 3D Printing
Adding colorants to resins is an essential part of the 3D printing process, which brings about its own considerations and challenges:
- How to add color to resins?
- What 3D printing resin colors are suitable for your product?
- What printing 3D methods are appropriate?
Therefore, we provide a thorough overview of how to add colorants to resin materials, so that you can make a sound decision for your coming projects.
How to add color to resin? Pigments explained
Coloring agents, such as pigments, can be directly incorporated into the liquid resin before the photopolymerization process. A pigment is a material that alters the color of reflected or transmitted light through wavelength-selective absorption. Put simply, it's a substance that appears a certain color because it absorbs specific wavelengths of light.
The primary purpose of using pigments is to impart color to the final product. These agents need to be compatible with the resin and should not hinder the curing process. Therefore, it is crucial to thoroughly mix the coloring agent into the resin to ensure an even color distribution.
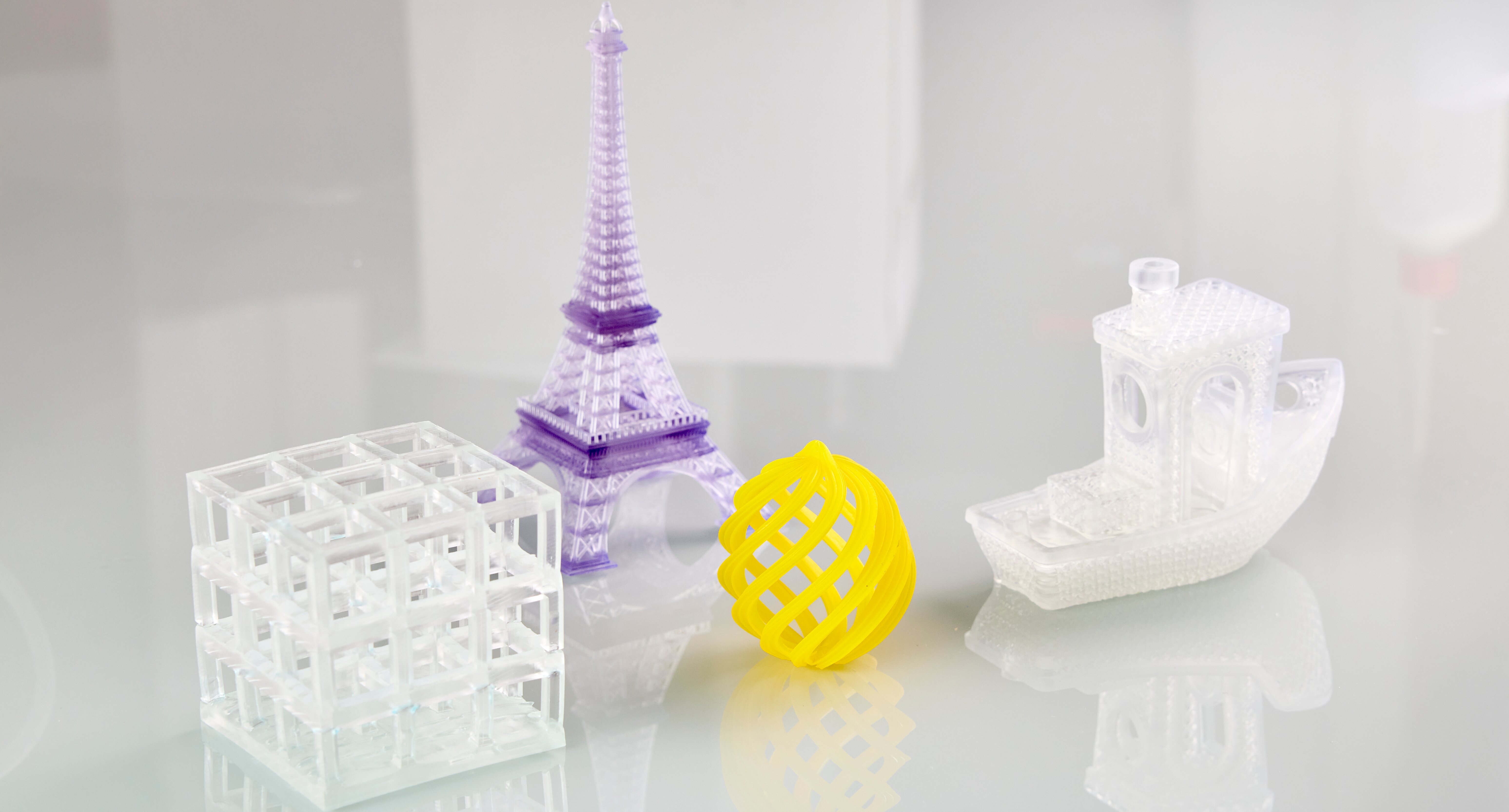
Organic vs inorganic pigments
Organic and inorganic pigments have both their advantages and are chosen based on factors such as color intensity, chemical stability, and cost, depending on the specific requirements of the application.
Organic pigments are derived from organic compounds, typically carbon-based molecules. They are often synthesised from petroleum-based chemicals or other natural sources. They tend to offer a wider range of bright and vivid colors compared to their inorganic counterparts.
Inorganic pigments, on the other hand, are naturally occurring or synthetically produced minerals or metal oxides. These pigments are known for their durability and lightfastness, making them suitable for applications where color stability is essential, such as automotive coatings, ceramics, and 3d printing construction materials. Inorganic pigments often exhibit more subdued and earthy tones compared to organic pigments.
Other 3D printing resin coloring methods explained
While adding custom coloring agents is the most common approach, there are other methods that customers can choose from.
Pre-colored photopolymers
Pre-colored photopolymers are formulated with pigments during their manufacturing process, resulting in a range of pre-tinted shades. This eliminates the necessity for additional coloring steps during usage. By integrating the desired color directly into the photopolymer, manufacturers ensure consistency and convenience for users.
These pre-colored formulations offer a straightforward solution for applications where specific colors are required, streamlining the production process and enhancing efficiency.
Manual painting
In certain instances, colored 3D prints might not achieve the desired level of detail or vibrancy. To address this, manual painting can be employed as a solution. This process involves applying acrylic, oil, or spray paint onto 3D printed parts.
While manual painting demands more time and effort compared to pre-colored prints, it offers an entirely customizable approach, which is suitable for prototypes or very specific color choices. This manual intervention provides flexibility and creative control over the final appearance of the printed object.
Common challenges of 3D printing resin colors
3D printing resin colors can't be chosen randomly, but the choice depends on the desired outcome of the printed product.
Uniform dispersion
Uniform dispersion is crucial for ensuring a consistent coloration in the final printed product. It ensures that each layer of the printed object receives an even coating, resulting in a visually consistent appearance without streaks or patches. This involves thoroughly mixing the colorant into the resin to prevent clumping or uneven distribution. Proper mixing techniques, such as agitation or stirring, help achieve a homogeneous mixture, minimising variations in color intensity or hue.
Material compatibility
Not all colorants are compatible with every material used. Factors such as chemical composition, molecular structure, and curing process can influence compatibility. Using incompatible colorants may lead to issues such as poor adhesion, reduced mechanical strength, brittleness or color distortion. Therefore, it's essential to select colorants specifically formulated for the intended resin to ensure optimal performance and color stability in the final printed product.
Curing properties
Colors can influence the original curing properties of 3D printing resins. Certain pigments used to color resins may absorb or reflect light differently, affecting the penetration depth of the curing light source. This can result in variations in curing time, depth, or overall strength of the printed object. Therefore, when selecting colorants for 3D printing resins, it's important to consider their impact on curing behavior to ensure consistent and reliable print quality.
Color stability
Some colorants used in 3D printing resins may degrade or undergo color changes when exposed to UV light or other environmental stressors. This degradation can result in fading, discoloration, or shifting of the printed object's color over time. Therefore, it's essential to select colorants with excellent UV stability and resistance to environmental factors to ensure long-term color retention and durability in 3D printed products, such as 3D-printed wearables.
Cost factor
Adding colors introduces an additional cost factor that needs to be considered and budgeted. The cost of 3D printing resin colors can vary depending on factors such as quality, concentration, and volume required for the desired coloration. Furthermore, the complexity of achieving consistent color dispersion and stability may require additional quality control measures, contributing to overall production costs.
3D printing resin colors: Common printing methods
Stereolithography (SLA) as well as Material Jetting are among the most commonly used methods when it comes to modern 3D printing. This section compares these printing methods with a focus on 3D printing resin colors.
Stereolithography (SLA)
Stereolithography (SLA) is an additive manufacturing process that utilises photopolymer resins cured by a UV laser to build 3D objects layer by layer. In SLA, colorants can be incorporated into the resin to achieve colored 3D prints. This is typically done by mixing pigments directly into the liquid resin before the printing process. By integrating colorants into the resin, SLA can produce intricately detailed and colored 3D prints suitable for a wide range of applications.
Material Jetting
Material Jetting is another additive manufacturing process where droplets of photopolymer resin are selectively deposited layer by layer onto a build platform using inkjet printheads. Pigments are often integrated into the photopolymer resin to enable the printing of colored objects. Similar to traditional inkjet printing, the printheads can dispense multiple colors of resin simultaneously, which is suitable for multicolor prototypes and product design applications.
Comparison: SLA vs. Material Jetting
SLA | MATERIAL JETTING | |
Description |
Liquid resin is solidified by a laser. |
Droplets of resin are cured by a printhead similar to an inkjet. |
Materials |
Photopolymers, 3D printing resin colors |
Photopolymers, 3D printing resin colors |
Applications |
Commonly used for rapid prototyping, producing highly detailed and accurate models with smooth surface finishes. |
Print with multiple materials and colors simultaneously, making it well-suited for creating realistic prototypes with complex geometries and vibrant colors |
Conclusion: Adding colors to resin requires a custom approach
Incorporating colors into resin needs a tailored approach to ensure optimal results. Factors such as material compatibility, curing properties, color stability, and cost must be carefully considered to achieve the desired outcome.
RAHN is your 3D printing solutions provider and reliable supply partner. Contact us to find out more about reliable printing solutions for a wide range of industries.
3D Printing Resin Colors: Frequently Asked Questions
1) What kind of colorants can be used to color a 3D resin?
Pigments are most commonly used. They serve a dual purpose of coloring the resin as well as improving resolution by reducing light bleed into the volume of liquid. Pigment pastes are commonly used as they are pre-dispersed which makes them easier to incorporate and less likely to settle out. Dyes can also be used.
2) Will adding colorants affect the performance of the 3D printed object?
Typically used in very low levels, colorants don't have a notable effect on mechanical properties. The most important effect is that they will reduce the penetration depth of light in photopolymers which can affect the print parameters as well as improve the resolution of the print itself. Depending on the type of pigment used, they can also cause ashes in casting or burn-out applications.
3) What can be done to eliminate pigment settling in a 3D resin?
To avoid pigment settling in 3D resin, it is crucial to use finely ground, high-quality pigments that are designed for resin applications. These pigments are specifically engineered to remain evenly dispersed throughout the resin. Regular stirring or shaking of the resin before use can help maintain a uniform color. Additionally, using pre-dispersed pigment pastes can significantly help with dispersion in the finished resin, ensuring even distribution and preventing settling. Dispersants can also be used to further stabilize the pigment, guaranteeing consistent results throughout the printing process.
Your personal contact
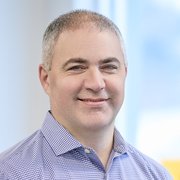
Christopher Cocklan
3D Printing Business Development Manager EnergyCuring
RAHN USA Corp.