How to
reduce brittleness of 3D resin prints
How to
reduce brittleness of 3D resin prints
Reducing Brittleness of Hard 3D Resin Prints
Brittleness is a common problem for photopolymer 3D resins. Making a formula that is hard is relatively easy. Making one that is hard, and durable takes extra effort and thought. Here we are defining durable as materials that show little or no change in properties over time. How the materials in a formula react, and the ultimate crosslink density are two keys to understanding how to improve durability.
In general, hard 3D photopolymer resins have limited conversion. This can be due to several factors including vitrification and the low intensity/exotherm of 3D printers.
As they age, these materials can tend to crack with or without exposure to light. While some additives can be used to alter the crosslink network to improve the durability, that route will also alter final print properties. Here we will discuss the roles of total (meth)acrylate functionality, and degree of post-curing in reducing brittleness.
First, we will examine the impact of post-cure. Dynamic Mechanical Analysis (DMA) can be used to quantitatively evaluate the effect of post-cure.
DMA of UV curable resins for 3D printing can highlight the differences between green properties (after simply washing the part and drying) and final properties (after wash/dry and post cure step). Tα,, the alpha transition, occurs when the network's large segments start moving. Post curing will shift the curves to higher temperatures for a given 3D resin, and there will be no change in properties after the final conversion is reached.
Incomplete curing leads to lower crosslinking. This may fake a higher flexibility, but it will also result in tackiness. It will also lead to lower HDT, strength and hardness. For a hard thermoset, lower crosslinking means higher chain length which leads to higher elongation.
A less measurable, but very influential, byproduct of incomplete cure is "dark polymerization", or a gradual change in properties over time. This can lead to a cured part with good initial properties to turn brittle over time.
An accelerated aging test can be performed to simulate dark polymerization and check for brittleness. An Arrhenius equation can help simulate long term aging in short time for faster reformulation.
Ageing done using a garlic-like thick round flat bottom model for easy printing and high internal stress:
- Printing using 385nm 3D printer
- Washed in isopropanol for 15min twice
- Post-cured with Xenon lamp for 2 hours
- One specimen at room tmeperature (RT)
- One specimen at 80°C for 3days
In our webinar Improving Toughness of Photopolymer 3D prints, we went into some detail on the role of cure as it relates to toughness. We also spoke on the behavior of monofunctional monomers and how they can add a degree of thermoplasticity to a 3D photopolymer resin.
The figure below visually shows those two concepts at work. Here we examine how modifying materials can affect brittleness of a hard Oligomer. Even with a higher degree of acrylate conversion (with aging), the monofunctional materials promote a lower overall crosslink density within the part, and thus less internal stress, leading to less cracking and brittleness.
There are several variables to consider when developing a hard 3D resin. Formulation and processing can be adapted to minimize internal stress and post-cure. Following the concepts highlighted here will help to deliver robust and more durable parts.
Looking for 3D printing solutions? Find out more about raw materials for 3D printing and get in touch
Your personal contact
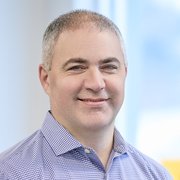
Christopher Cocklan
3D Printing Business Development Manager EnergyCuring
RAHN USA Corp.