High-Strength
3D Printing Resins
High-Strength
3D Printing Resins
A Comparative Analysis of High-Strength 3D Printing Resins
The strongest material for 3D printing mainly depends on the desired properties of the final product. From tensile and flexural strength to impact and heat resistance – photopolymer resins can be customised depending on the material needs. We explain specific properties, examples and applications for the strongest 3D printing resin.
What is the strongest material for 3D printing?
When determining the strongest material for 3D printing, it is important to look at the intended purpose and application of the final product. For instance, 3D printing in the automotive industry has different requirements compared to 3D printing in dentistry, even though both products need to be highly durable.
Therefore, determining the strongest material depends on the specific requirements of the intended application, considering factors like tensile strength, impact resistance, heat tolerance, and other mechanical properties.
Based on the desired properties, the materials can be engineering-grade resins, reinforced photopolymers, dental resins or resins for medical devices, just to name a few. Each specific resin excels in different aspects, catering to diverse industrial needs.
Properties determining the strongest 3D printing resin
The strongest 3D printing resin can take many forms. The following section describes properties, which are commonly referred to as strong and durable.
Tensile strength
Tensile strength refers to the maximum stress that a material can endure while being stretched or pulled before it breaks or permanently deforms. It's a crucial mechanical property used to evaluate the durability and suitability of materials for various applications.
Industries such as aerospace, automotive, 3D printing in construction, engineering, and 3D printing in healthcare rely heavily on materials with high tensile strength for 3D printing applications. For instance, in aerospace, parts need to withstand extreme conditions while remaining lightweight.
In the automotive industry, 3D printing with materials possessing good tensile strength helps create robust prototypes and functional parts for vehicles that can handle mechanical stress during testing and actual use. .
Flexural strength
Flexural strength, also known as bend strength, measures a material's ability to resist deformation or fracture when subjected to bending forces.
Next to aerospace or automotive industries, various consumer products, such as sports equipment, toys, and household items, profit from flexural strength, which ensures the durability and resilience against bending or twisting.
Photopolymer-based materials are extensively used in dentistry for creating crowns, bridges, and dentures. These materials need adequate flexural strength to withstand the forces exerted during biting and chewing without fracturing.
Impact resistance
Impact resistance refers to a material's ability to withstand sudden or dynamic loads or shocks without breaking or fracturing. It measures how much energy a material can absorb before rupturing or deforming under sudden force.
Equipment in sports and recreation, such as helmets, protective gear and sporting goods, require high impact resistance to protect users from potential injuries during collisions.
Products like smartphone cases, electronic device housings, and other consumer electronics benefit equally from impact-resistant materials to ensure durability and to protect the internal components from damage due to accidental drops.
Heat resistance
Heat resistance describes a material's ability to withstand elevated temperatures without significant degradation, softening, melting, or structural damage. This property is crucial in applications where exposure to elevated temperatures is a significant factor.
Within the automotive sector, 3D printing is used for producing parts like engine components, exhaust systems, and heat shields. Heat-resistant materials are essential to maintain structural integrity and functionality under these high-temperature conditions.
Processes requiring tooling or moulds, such as injection moulding or casting, equally require heat-resistant materials.
Dimensional stability
Dimensional stability is a material's ability to maintain its intended shape and size when subjected to various environmental conditions, such as changes in temperature, humidity, or stress.
Industries using 3D printing for creating functional prototypes, tooling, and production parts rely on dimensional stability. Ensuring that printed parts maintain precise dimensions is crucial for proper fit, assembly, and functionality within machinery and equipment.
In medical applications, such as patient-specific implants or prosthetics, dimensional stability is essential for ensuring a precise fit and proper functionality within the human body.
Layer adhesion
Layer adhesion refers to the strength of bonding between individual layers of material in a 3D printed object. A strong layer adhesion is essentially necessary for all applications, as it ensures the overall longevity of printed objects.
Both aerospace and automotive industries benefit from 3D printing for producing lightweight yet robust parts. Strong layer adhesion is essential in creating components like brackets, housings, and prototypes that can withstand the demanding conditions and stresses experienced in these sectors.
Applications in the medical field equally rely on a strong layer adhesion to ensure the integrity and reliability of the printed medical devices.
Examples of the strongest photopolymer resins for 3D printing
3D printing photopolymer resins are custom-made to specific requirements and can be categorized according to their composition of properties.
Engineering-grade resins
Engineering-grade resins offer a combination of properties that provide reliability, durability, and stability for 3D-printed parts in industries such as aerospace, automotive, medical, and manufacturing. In these industries, robust materials are essential for demanding applications. The ability to meet stringent performance criteria makes these resins the strongest material for 3D printing, as they contribute to durable and reliable printed parts in challenging environments.
- High tensile strength
- High flexural strength
- Heat resistance
- Chemical resistance
- Dimensional stability
- Impact resistance
Reinforced photopolymer resins
3D printing photopolymer composites, including those produced through techniques such as Vat photopolymerization, combines photopolymer resins with reinforcing agents like fibres or particles, enhancing their mechanical properties. The specific properties can vary based on the type and concentration of reinforcements used. Key characteristics often associated with reinforced photopolymer resins include tensile and flexural strength, stiffness, dimensional stability and impact resistance.
- High tensile strength
- High flexural strength
- Stiffness
- Dimensional stability
- Impact resistance
Dental Resins
Dental resins undergo rigorous testing and formulation to meet specific criteria essential for oral applications. These resins exhibit a range of properties crucial for dental procedures and prosthetic fabrication, including biocompatibility, tensile and flexural strength, durability, low shrinkage and chemical resistance. These properties collectively ensure that dental resins are suitable for various applications, including crowns, bridges, dentures, and orthodontic appliances.
- Biocompatibility
- High tensile strength
- High flexural strength
- Durability
- Low shrinkage
- Chemical resistance
Resins for medical devices
Similar to dental resins, resins used in 3D printing in healthcare need to fulfil a wide range of standards related to safety, reliability, and performance in healthcare settings. The required properties make these resins suitable for manufacturing medical devices such as implants, surgical instruments, catheters, and prosthetics.
- Biocompatibility
- Flexibility
- High tensile strength
- High flexural strength
- Sterilisation compatibility
- Chemical resistance
- Adhesion
Examples for the strongest material for 3D printing in healthcare
RAHN's GENOMER* 4267 urethane acrylate excels in impact resistance and adheres well to carbon steel, aluminium and stainless steel. Its weathering performance ensures resistance against yellowing, cracking and gloss reduction. It also delivers exceptional bonding capabilities and resistance characteristics.
The ability to seamlessly integrate with urethane acrylates, polyester or epoxy acrylates as well as acrylate monomers makes it suitable for a wide range of applications. GENOMER* 4267 offers reliability and longevity, making it an excellent choice for various medical device applications.
Find out more about how to improve resin strength: Enhancing 3D Resin Strength with GENOMER* 4293 & 4247.
Customise your high-strength 3D printing resins
The strongest material for 3D printing depends solely on your requirements. RAHN offers tailor-made 3D printing solutions in close collaboration with our customers to attain the desired results. Achieve outstanding performance and durability by harnessing our expertise in formulating resins suited to your individual needs.
Your personal contact
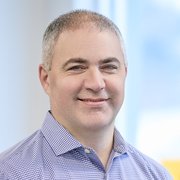
Christopher Cocklan
3D Printing Business Development Manager EnergyCuring
RAHN USA Corp.